Graphite Display
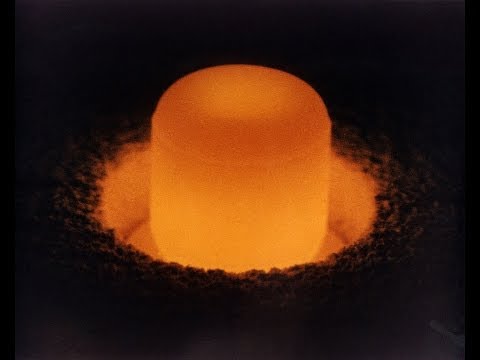
Historian Alex Wellerstein introduces Plutonium, the element named after Pluto, a far-out planet and the Roman god of death.
Narrator: When it comes to cool new advances, nuclear science has always boasted some of the most far out discoveries. When the heaviest element found in nature was discovered, the farthest away known planet was Uranus, and so the element was named uranium. By the time an element heavier than uranium was created, there was a new farthest out planet, Neptune, and Neptunium was born. And by the time they discovered an element heavier still, Pluto still held planetary status and we had plutonium.
Alex Wellerstein: Plutonium is a manmade substance. It is an element that generally speaking does not exist in nature. It is just stable enough to be something we can keep around, but it is also just unstable enough that we can use it inside a nuclear bomb. It is really tricky metal, probably appropriately named plutonium for Pluto, originally a planet but also the Roman god of death.
Narrator: Plutonium is prone to both chemical and physical changes with shifts in temperature. And it is both radioactive and toxic. What is more, it is pyrophoric, meaning it can catch fire when it is exposed to air.
Alex Wellerstein: Glenn Seaborg, when he discovered it, gave it the atomic abbreviation of Pu, not Pl. And it was partially as a joke because plutonium was so difficult and somewhat nasty to work with. So it is “P-U.”
Narrator: Of course, plutonium was essential to the wartime bomb effort, and despite its challenges it continues to find useful applications today such as fueling space exploration vehicles like the Curiosity Rover sent to Mars. After all these years, plutonium is still one far out element.
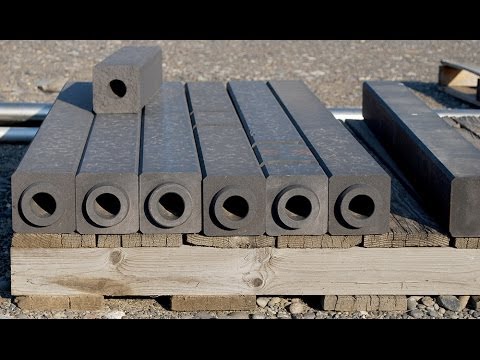
Hanford engineer Gene Woodruff explains the precision required to make the 70,000 graphite bars for the B Reactor.
Narrator: Constructing every part of the B Reactor required great precision. Nowhere was this more important than the manufacture and milling of the reactor’s 70,000 graphite bars. With main ingredients petroleum coke and tar pitch, the recipe for nuclear graphite required intense heat for sustained periods to drive out impurities. The process took nearly two weeks, and included three bakes at temperatures reaching 2800 degrees Celsius. Luckily, the steel industry had something called the Acheson furnace that could muster the heat and handle the load. In Oak Ridge, Tennessee, a small-scale graphite reactor, the X-10, was built to test the new graphite machining techniques. That knowledge was then transported to a location near Hanford High School.
Gene Woodruff: The machine shop had preceded it, from the East Coast. It was originally set up at Oak Ridge to machine graphite for the X-10 Reactor. When that was done, they shipped the machinery and the personnel to Hanford to machine Hanford graphite.
Narrator: It was exacting work. Each and every one of the thousands of blocks had to be accurate to within five one-thousandths of an inch. Even a slight variation could change the rate at which neutrons were absorbed.
Gene Woodruff: They had what they called a dance floor next to the machine shop. The finished bars were laid up in the same sequence that would be laid up in the reactor, then reassembled on pallets in the reverse order that they would go into the reactor.
Narrator: At the reactor site, shielding walls 40 feet high were erected in preparation for the finished graphite’s arrival.
Gene Woodruff: The graphite was slid down off of the pallet onto the floor and then slid over to the position it was going to go into. This generated a little bit of graphite dust. Part of the crew was running vacuum cleaners over the surface that they were walking on. If they had left a dust film on there and they got 100 layers up in the air, they would probably find that the tube they were trying to push through the shielding did not really line up with the hole it was supposed to go in. So the vacuum was a very critical part of that clean up.
Narrator: But with surgical precision and cleanliness, the crew managed to line up every block with pinpoint accuracy, making it possible for the B Reactor to write its chapter in history.
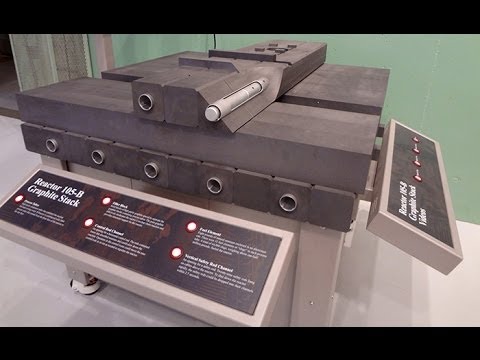
Hanford engineer Gene Woodruff explains how the layers of graphite blocks inside the B Reactor’s core were very carefully stacked.
Narrator: We built this cool display to show how the 70,000 graphite blocks are assembled. Gene Woodruff will guide us through the model, starting with the bottom layer of alternating tube and filler blocks.
Gene Woodruff: The tube blocks were the blocks that had the process tubes and the fuel running actually through them. And the neighboring blocks were called filler blocks, and they were solid graphite blocks that were the moderating material in the reactor. In the tube layers, both tube blocks and filler blocks, the corners were leveled off. Angling those corners was called chamfering. The chamfered corners on those blocks created small openings for channels through the stack that allowed the helium atmosphere to move through the reactor.
Let’s go to the next layer, the filler layer. These bars are arranged across the tube layers. They crisscross all the way through the reactor. In the model, there is one channel open, and that was for a horizontal control rod. The blocks you can see on either side of that are locked in place with small graphite keys. That was the method used throughout the reactor to stabilize the structure. Those keys were very tight-fitting, very close tolerance.
The next layer up is a tube layer again. It is arranged front to rear, and it has a cutaway exposing a cooling tube. And a fuel element, or in old terminology, a slug, is shown. There were about 24 of those in a tube, and filler pieces in front and rear to center the fuel in the center part of the reactor. On the top layer, you can see small quarter-inch diameter holes drilled in an angle that penetrate down to the central tube bore, and this aided in the helium gas distribution throughout the reactor. It aided in the ability of the gas to pick up water vapor or leaks from a potentially leaking tube.
In the back portion of that layer, there is a vertical opening in the reactor for the safety rod access into the core of the reactor. These safety rods were hung above the reactor on cables in case there was a need for an immediate shut down. A second or two it would take to get the rods fully inserted in the reactor.
Narrator: With millions of lives riding on the B Reactor’s results, every piece in this intricate design was precisely milled and painstakingly assembled. It was exactly what the war effort needed.