Oak Ridge, TN
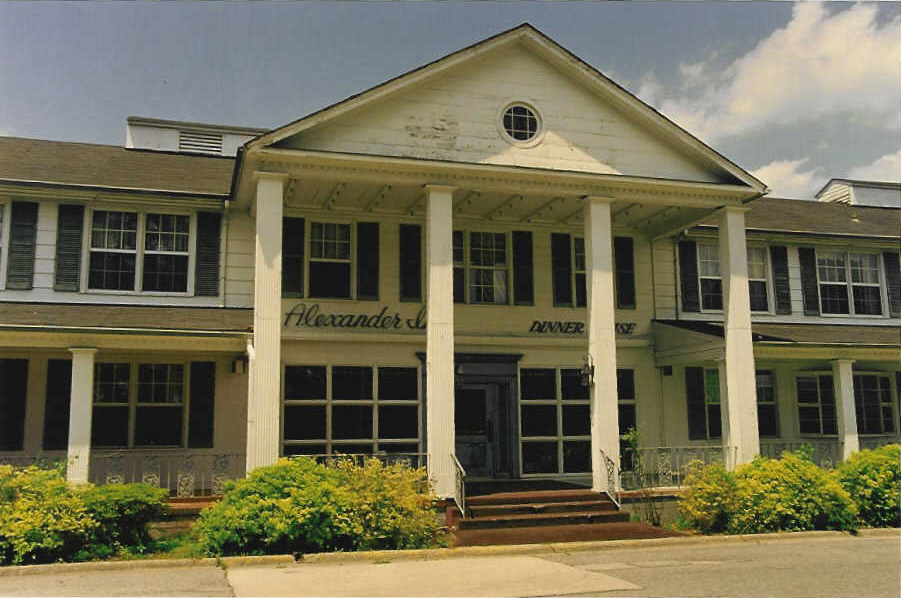
Oak Ridge was the home of the uranium enrichment plants (K-25 and Y-12), the liquid thermal diffusion plant (S-50), and the pilot plutonium production reactor (X-10 Graphite Reactor).
Site Selection
In 1942, General Leslie Groves approved Oak Ridge, Tennessee, as the site for the pilot plutonium plant and the uranium enrichment plant. Manhattan Project engineers had to quickly build a town to accommodate 30,000 workers–as well as build the enormously complex plants.
By the time President Roosevelt authorized the Manhattan Project on December 28, 1942, work on the east Tennessee site where the first production facilities were to be built was already underway. On Saturday, September 19, Groves had approved the acquisition of 59,000 acres of land along the Clinch River, 20 miles west of Knoxville, Tennessee. Also approved was the removal of the relatively few families on the marginal farmland and extensive site preparation to provide the transportation, communications, and utility needs of the town and production plants that would occupy the previously undeveloped area. At first, this location was known as “Site X” and later changed to the Clinton Engineer Works, named after the nearest town. After the war, the name was again changed officially to Oak Ridge.
Building Oak Ridge
Original plans called for the military reservation to house approximately 13,000 people in prefabricated housing, trailers, and wood dormitories. By the time the Manhattan Engineer District headquarters were moved from Washington, DC to Tennessee in the summer of 1943 (Groves kept the Manhattan Project’s office in Washington and placed Col. Kenneth D. Nichols in command at Tennessee), estimates for the town of Oak Ridge had been revised upward to 45,000 people. By the end of the war, Oak Ridge was the fifth largest city in Tennessee. While the Army and its contractors tried desperately to keep up with the rapid influx of workers and their families, services always lagged behind demand.
The town site was in the northeast corner of the reservation, a strip less than one mile wide and six miles long with hilly terrain descending from the Black Oak Ridge in the north. Town planners were originally to provide housing for an estimated 30,000 people, but by 1945, the population had reached 75,000. Architectural firm Skidmore, Owings & Merrill (SOM) envisioned pleasant neighborhood communities with libraries, schools and shopping centers. However, wartime constraints limited the availability of labor and materials. Rather than performing time-consuming grading, houses were adjusted to fit the contours of the land. Most of Oak Ridge’s kitchens faced the street to minimize the length of plumbing and utility lines.
Life at Oak Ridge
Materials were in short supply, so the first houses were built of prefabricated panels of cement and asbestos or cemesto board. They were known as “alphabet houses” because each of the handful of home designs was assigned a letter of the alphabet. There were small, two bedroom “A” houses, “C” houses with extra bedrooms, “D” houses with a dining room, and so forth for a total of 3,000 cemesto-type homes. Later, thousands of prefabricated houses were sent to Oak Ridge in sections complete with walls, floors, room partitions, plumbing and wiring. Workers turned over 30 or 40 houses to occupants each day. The Roane-Anderson Company administered all housing facilities.
Part of Oak Ridge’s appeal to Manhattan Project planners was nearby Knoxville with its population of 111,000. However, the top-secret project was not warmly welcomed in Knoxville, arousing both suspicion and resentment. Many saw the people flooding into East Tennessee from all over the country—and the world—as “furriners” who could not be questioned. In a time of austerity and rationing, others resented Oak Ridge residents arriving with unlimited ration stamps and fistfuls of cash. Oak Ridgers who ventured into Knoxville were easy to spot. The quickly constructed secret city was blanketed in a thick layer of mud. As a result, its residents’ muddy shoes were a dead giveaway as to their origin.
The Plants
The four production facility sites were located in valleys away from the town. This provided security and containment in case of accidental explosions. The Y-12 area, home of the electromagnetic plant, was closest to Oak Ridge, being one ridge away to the south. Farther to the south and west lay both the X-10 area, which contained the experimental plutonium pile and separation facilities, and K-25, site of the gaseous diffusion plant and later the S-50 thermal diffusion plant.
X-10 Graphite Reactor
The X-10 Graphite Reactor was the first reactor built after the successful experimental “Chicago Pile I” at the University of Chicago. On December 2, 1942, using a lattice of graphite blocks and uranium rods, Enrico Fermi proved that a nuclear chain reaction could be controlled. Scientists knew that it would only be a matter of time before the energy of the atom could be harnessed for a bomb.
Purpose
The X-10 Graphite Reactor was a semi-works (pilot plant) facility based on design and engineering information developed at the Metallurgical Laboratory at the University of Chicago. Based on Fermi’s pile (CP-1), the X-10 Reactor and associated chemical extraction facility, produced the world’s first plutonium outside the laboratory. Technology developed at Oak Ridge formed the foundation upon which the giant plutonium producing facilities at Hanford were based.
DuPont broke ground for the X-10 complex at Oak Ridge in February 1943. The site would include an air-cooled experimental pile reactor, a pilot chemical separation plant, and various support facilities. Cooper produced blueprints for the chemical separation plants in time for construction to begin in March. A series of huge underground concrete cells, the first of which sat under the pile, extended to one story above ground. Aluminum cans containing uranium slugs would drop into the first cell of the chemical separation facility and dissolve and then begin the extraction process.
The pile building itself went up during the spring and summer of 1943, a huge concrete shell seven feet thick with hundreds of holes for uranium slug placement. Slugs were to plutonium piles what barrier was to gaseous diffusion; that is, an obstacle that could shut down the entire process. ALCOA (Aluminum Company of America) was the only firm left working on a process to enclose uranium 235 within aluminum sheaths, and it was still having problems. Initial production provided mixed results, with many cans failing vacuum tests because of faulty seams.
Going Critical
The moment everyone had been waiting for came in late October 1943 when DuPont completed construction and tests of the X-10 pile. After thousands of uranium slugs were loaded, the pile went critical in the early morning of November 4th and produced its first plutonium by the end of the month. Criticality was achieved with only half of the channels filled with uranium. During the next several months, Compton gradually raised the power level of the pile and increased plutonium yield.
Chemical separation techniques using the bismuth phosphate process were so successful that Los Alamos received its first plutonium samples beginning in the spring of 1944. Fission studies of these samples at Los Alamos during the summer heavily influenced bomb design.
After the War
In 1946, X-10 began producing peacetime radioisotopes for use in industry, agriculture, medicine and research. The pile was permanently shut down in 1963 and designated a National Historic Landmark in 1966 and a National Historic Chemical Landmark in 2008. The reactor has also been recently renovated and is often included in tours provided by ORNL to visitors.
Y-12 Plant
The Y-12 Plant in Oak Ridge used the electromagnetic separation method, developed by Ernest Lawrence at University of California-Berkeley, to separate uranium isotopes, and was the most developed way to produce fissile material at the start of the Manhattan Project. When an electrically-charged atom was placed in a magnetic field, it would trace a circular path with a radius determined by the atom’s mass. U-235 was lighter than U-238 and could be isolated by placing a collecting pocket in its path.
Although the Lewis Committee report had placed gaseous diffusion ahead of the electromagnetic approach, many were still betting in early 1943 that Lawrence and his mass spectrograph would eventually predominate. Lawrence and his laboratory of mechanics at Berkeley continued to experiment with the giant 184-inch magnet, trying to reach a consensus on which shims, sources, and collectors to incorporate into the Y-12 design for the Oak Ridge plant. Research on magnet size and placement and beam resolution eventually led to a “racetrack” configuration of two magnets with forty-eight gaps containing two vacuum tanks each per building, with ten buildings being necessary to provide the 2,000 sources and collectors needed to separate 100 grams of uranium 235 daily. It was hoped that improvements in calutron design, or placing multiple sources and collectors in each tank, might increase efficiency and reduce the number of tanks and buildings required, but experimental results were inconclusive even as Stone & Webster of Boston, the Y-12 contractor, prepared to break ground.
Planning the Plant
At a meeting of Groves, Lawrence, and John Lotz of Stone & Webster in Berkeley late in December 1942, Y-12 plans took shape. It was agreed that Stone & Webster would take over design and construction of a 500-tank facility, while Lawrence’s laboratory would play a supporting role by supplying experimental data. By the time another summit conference on Y-12 took place in Berkeley on January 13 and 14, Groves had persuaded the Tennessee Eastman Company to sign on as plant operator and arranged for various parts of the electromagnetic equipment to be manufactured by the Westinghouse Electric Company, the Allis-Chalmers Manufacturing Company and the Chapman Valve Manufacturing Company. At the same time, General Electric agreed to provide electrical equipment.
On January 14, after a day of presentations and a demonstration of the experimental tanks in the cyclotron building, Groves stunned the Y-12 contractors by insisting that the first racetrack of ninety-six tanks be in operation by July 1 and that 500 tanks be delivered by year’s end. Given that each racetrack assembly was 122 feet long, 77 feet wide and 15 feet high, the completed plant was to be the size of three, large two-story buildings, tank design was still in flux, and chemical extraction facilities also would have to be built, Groves’ demands were little less than shocking. Nonetheless, Groves maintained that his schedule could be met.
For the next two months Lawrence, the contractors, and the Army negotiated over the final design. While all involved could see possible improvements, there simply was not enough time to incorporate every suggested modification. Y-12 design was finalized at a March 17 meeting in Boston, with one major modification – the inclusion of a second stage of the electromagnetic process. The purpose of this second stage was to take the enriched uranium 235 derived from several runs of the first stage and use it as the “feed material” for a second stage of racetracks containing tanks approximately half the size of those in the first. Groves approved this arrangement and work began on both the Alpha (first-stage) and Beta (second-stage) tracks.
Breaking Ground
Groundbreaking for the Alpha plant took place on February 18, 1943. Soon blueprints could not be produced fast enough to keep up with construction as Stone & Webster labored to meet Groves’ deadline. The Beta facility was actually begun before formal authorization. While laborers were aggressively recruited, there was always a shortage of workers skilled enough to perform jobs according to the rigid specifications. (A further complication was that some tasks could be performed only by workers with special security clearances). Huge amounts of material had to be obtained (38 million board feet of lumber, for instance), and the magnets needed so much copper for windings that the Army had to borrow close to 15,000 tons of silver bullion from the United States Treasury to fabricate into strips and wind onto coils as a substitute for copper. Treasury silver was also used to manufacture the busbars that ran around the top of the racetracks.
Replacing copper with silver solved the immediate problem of the magnets and busbars, but persistent shortages of electronic tubes, generators, regulators, and other equipment plagued the electromagnetic project and posed the most serious threat to Groves’ deadline. Furthermore, last minute design changes continued to frustrate equipment manufacturers. Nonetheless, when Lawrence toured with Y-12 contractors in May of 1943, he was impressed by the scale of operations. Lawrence returned to Berkeley rededicated to the “awful job” of finishing the racetracks on time.
Lawrence and his colleagues continued to look for ways to improve the electromagnetic process. Lawrence found that hot (high positive voltage) electrical sources could replace the single cold (grounded) source in future plants, providing more efficient use of power, reducing insulator failure, and making it possible to use multiple rather than single beams. Meanwhile, receiver design evolved quickly enough in spring and summer 1943 to be incorporated into the Alpha plant. Work at the Radiation Laboratory picked up additional speed in March with the authorization of the Beta process. With Alpha technology far from perfected, Lawrence and his staff now had to participate in planning for an unanticipated stage of the electromagnetic process.
Racing Against Time
While the scientists in Berkeley studied changes that would be required in the down-sized Beta racetracks, engineering work at Oak Ridge prescribed specific design modifications. For a variety of reasons, including simplicity of maintenance, Tennessee Eastman decided that the Beta plant would consist of a rectangular, rather than oval, arrangement of two tracks of thirty-six tanks each. Factoring this configuration into their calculations, Lawrence and his coworkers bent their efforts to developing chemical processing techniques that would minimize the loss of enriched uranium during Beta production runs. To make certain that Alpha had enough feed material, Lawrence arranged for research on an alternate method at Brown University and expanded efforts at Berkeley. With what was left of his time and money in early 1943 Lawrence built prototypes of both Alpha and Beta units at Berkeley for testing and training operating personnel. Meanwhile Tennessee Eastman, running behind schedule, raced to complete experimental models so that training and test runs could be performed at Oak Ridge.
But in the midst of encouraging progress in construction and research on the electromagnetic process in July came discouraging news from Oppenheimer’s isolated laboratory in Los Alamos, set up in 1943 to consolidate work on atomic weapons. Oppenheimer warned that three times more fissionable material would be required for a bomb than earlier estimates had indicated. Even with satisfactory performance of the racetracks, it was now possible that they might not produce enough purified uranium 235 in time.
Lawrence responded to this crisis in characteristic fashion: He immediately lobbied Groves to incorporate multiple sources into the racetracks under construction and to build even more racetracks. Groves decided to build the first four as planned but, after receiving favorable reports from both Stone & Webster and Tennessee Eastman, allowed a four-beam source in the fifth. Convinced that the electromagnetic process would work and sensing that estimates from Los Alamos might be revised downward in the future, Groves let Lawrence talk him into building a new plant – in effect, doubling the size of the Y-12 complex. The new facility, Groves reported to the Military Policy Committee on September 9, would consist of two buildings, each with two rectangular racetracks of ninety-six tanks operating with four-beam sources.
Setbacks
During the summer and fall of 1943 the first electromagnetic plant began to take shape. The huge building to house the operating equipment was readied as manufacturers began to deliver everything from electrical switches to motors, valves, and tanks. While construction forces now totaled more than 15,000 people, another 5,000 operating and maintenance personnel were hired and trained. Then between October and mid-December, Y-12 paid the price for being a new technology that had not been put through its paces in a pilot plant. Vacuum tanks in the first Alpha racetrack leaked and shimmied out of line due to unforeseen tremendous magnetic forces, welds failed, electrical circuits malfunctioned, and operators made frequent and costly mistakes. Most seriously, the magnet coils shorted out because of rust and sediment in the cooling oil.
Groves arrived on December 15 and shut the entire racetrack down. The coils were sent back to Allis-Chalmers with hope that they could be cleaned without being dismantled entirely, while measures were taken to prevent recurrence of the shorting problem. The second Alpha track now bore the weight of the electromagnetic effort. In spite of precautions aimed at correcting the electrical and oil related problems that had shut down Alpha 1, the second Alpha fared little better when it started up in mid-January 1944. While all tanks operated at least for short periods, performance was sporadic and maintenance could not keep up with the electrical failures and defective parts. Like its predecessor, Alpha 2 was a maintenance nightmare.
Alpha 2 eventually produced about 200 grams of twelve-percent uranium 235 by the end of February 1944, enough to send samples to Los Alamos as well as feed the new Beta unit but not enough to satisfy estimates of weapon requirements. The first four Alpha tracks did not operate together until April, a full four months behind schedule. While maintenance improved, output was well under previous expectations. The opening of the Beta building on March 11, 1944 led to further disappointment. Beam resolution was so unsatisfactory that a complete redesign was required. To make matters worse, word spread that the K-25 gaseous diffusion process was in deep trouble because of its ongoing barrier crisis. K-25 had been counted upon to provide uranium enriched enough to serve as feed material for the Beta tracks. Now it would be producing such slight enrichment that the Alpha tracks would have to process K-25’s material, requiring extensive redesign and retooling of tanks, doors and liners, particularly in units that would be wired to run as hot, rather than as cold electrical sources.
Expanding Y-12
It became clear to Groves that he would have to find a way for a combination of isotope separation processes to produce enough fissionable material for bombs. This meant making changes in the racetracks so that they could process the slightly enriched material that was being produced at K-25. He then concentrated on further expansion of the electromagnetic facilities. Lawrence, seconded by Oppenheimer, believed that four more racetracks should be built to accompany the nine already finished or under construction. Groves agreed with this approach, though he was not sure that the additional racetracks could be built in time to make a difference.
As the K-25 stock continued to drop and plutonium prospects remained uncertain, Lawrence lobbied yet again for further expansion of Y-12, arguing that it provided the only possible avenue to a bomb by 1945. His plan was to convert all tanks to multiple beams and to build, yet again, two more racetracks. By this time even the British had given up on gaseous diffusion and urged acceptance of Lawrence’s plan.
Time was quickly running out, and an element of desperation crept into decisions made at a meeting on July 4, 1944. Groves met with the Oak Ridge contractors to consider proposals Lawrence had prepared after assessing once again the resources and abilities of the Berkeley Radiation Laboratory. There was to be no change in the completed racetracks; there simply was not enough time. Some improvements were to be made in the racetracks then under construction. In the most important decision made at the meeting, Lawrence was to throw all he had into a completely new type of “calutron” that would use a thirty-beam source. Technical support would come from both Westinghouse and General Electric, which would cease work on four-beam development. It was a gamble in a high-stakes game, but sticking with the Alpha and Beta racetracks might have been an even greater gamble.
K-25 Plant
The K-25 Plant in Oak Ridge, TN housed the massive gaseous diffusion apparatus used to partially enrich uranium before it was sent to the nearby Y-12 Plant. “K-25” comes from Kellex Corporation, the contractor that designed and built the plant, and uranium-235, often shortened to “25.” The K-25 plant was an enormously ambitious and risky undertaking. A mile-long, U-shaped building, the K-25 plant was the world’s largest roofed building at the time. British scientists working on the “tube alloy,” code for the atomic bomb project, first advocated the gaseous diffusion method in March 1941. Because of the Nazi bombing of England, any production plants had to be located elsewhere.
Columbia University’s John R. Dunning and Eugene Booth began working in 1941 on the gaseous diffusion process. The goal was to separate the isotopes of U-235 from U-238 by turning uranium metal into uranium hexaflouride gas and pumping it through a barrier material that had millions of microscopic holes. Developing an effective barrier material was the greatest challenge. Columbia University’s SAM Labs, Kellex Corporation, and Union Carbide all pursued major programs addressing this very difficult problem, and all contributed to its final solution. General Groves ordered construction to begin and the plant was one-third complete before a solution was found.
Planning the Plant
Eleven miles southwest of Oak Ridge on the Clinch River was the site of the planned K-25 Gaseous Diffusion plant upon which so much hope had rested when it was authorized in late 1942. Championed by the British and placed first by the Lewis Committee, gaseous diffusion seemed to be based on sound theory but had not yet produced any samples of enriched uranium-235.
At Oak Ridge, on a relatively flat area of about 5,000 acres, site preparation for the K-25 power plant began in June. Throughout the summer, contractors contended with primitive roads as they shipped in the materials needed to build what became the world’s largest steam electric plant. In September work began on the cascade building, plans for which had changed dramatically since the spring. Now there were to be fifty four-story buildings (2,000,000 square feet) in a U-shape measuring a half-mile long by 1,000 feet wide. Innovative foundation techniques were required to avoid setting thousands of concrete piers to support load-bearing walls.
Since it was eleven miles from the headquarters at Oak Ridge, the K-25 site developed into a satellite town. Housing was supplied, as was a full array of service facilities for the population that eventually reached 15,000. Dubbed “Happy Valley” by the inhabitants, the town had housing similar to that in Oak Ridge, but, like headquarters, it too experienced chronic shortages. Even with a contractor camp with facilities for 2,000 workers nearby, half of the construction force had to commute to the site daily.
K-25 cost $512 million to build, or $6.5 billion in 2010 dollars. The mile-long, U-shaped plant covered forty-four acres, was four stories high and up to 400 feet wide. Engineers developed special coatings for the hundreds of miles of pipes and equipment to withstand the corrosive uranium hexaflouride gas that would pass through the plant’s 3,000 repetitive diffusion stages (together making up a cascade).
The entire process was hermetically sealed like a thermos bottle, as any moisture could cause a violent reaction with the uranium hexafluoride. Even minute pinhole leaks and contamination from fingerprints were major concerns. A special leak detector was invented and every component of the entire system underwent a “cleanliness control” procedure before it was installed.
Downgrading K-25
In late summer of 1943 it was decided that K-25 would play a lesser role than originally intended. Instead of producing fully enriched uranium 235, the new gaseous diffusion plant would provide around fifty-percent enrichment for use as feeder material for Y-12. This would be accomplished by eliminating the more troublesome upper part of the cascade. Even this level of enrichment was not assured since a suitable barrier for the diffusion process still did not exist. The decision to downgrade K-25 was part of the larger decision to double the capacity of Y-12 and fit with Groves’ new strategy of utilizing a combination of separation methods to produce enough fissionable material for bombs as soon as possible.
There was no doubt in Groves’ mind that gaseous diffusion still had to be pursued vigorously. Not only had major resources already been expended on the program, but there was also the possibility that it might yet prove successful. Y-12 was in trouble as 1944 began, and the plutonium pile projects (X-10) were just getting underway. A workable barrier design might put K-25 ahead in the race for the bomb. Unfortunately, no one had been able to fabricate barrier material of sufficient quality. The only alternative remaining was to increase production enough to compensate for the low percentage of barrier that met specifications. As Lawrence prepared to throw everything he had into a thirty-beam source for Y-12, Groves ordered a crash barrier program, hoping to prevent K-25 from standing idle as the race for the bomb continued.
After the War
The K-25 plant was more reliable and efficient than anyone predicted. After the war, the K-25 was expanded with the K-27, K-29, K-31 and K-33 plants built as additional stages of the process. The plants produced the majority of the U-235 for the Cold War arsenal. The K-25 plant was the first large-scale fully automated factory in history. Because of the complexity and size of the plant, 9,000 employees working in three shifts were needed to monitor its operations.
Until 1985, K-25 produced fuel for civilian nuclear power reactors around the world. In addition, K-25 developed a commercially competitive gas centrifuge technology. K-25’s innovative technologies served the nation in World War II and the Cold War with great distinction.
S-50 Plant
The theory behind investing in S-50 was that the enrichment process might work best if the three plants were used in a series. In practice, this proved to be correct. The uranium product was slightly enriched at S-50 (one to two percent U-235) and this was fed into the K-25 plant. The gaseous diffusion process raised the enrichment to about 20 percent. This was fed into the Y-12 plant for the final enrichment cycle. Through this serial approach, the first atomic bomb received its enriched uranium.
Oppenheimer Gets Involved
As problems with both Y-12 and K-25 reached crisis proportions in the spring and summer of 1944, the Manhattan Project received help from an unexpected source – the United States Navy. President Roosevelt had instructed that the atomic bomb effort be an Army program and that the Navy be excluded from deliberations. Navy research on atomic power, conducted primarily for submarines, received no direct aid from Groves, who, in fact, was not up-to-date on the state of navy efforts when he received a letter on the subject from Oppenheimer in April 1944.
Oppenheimer informed Groves that Philip Abelson’s experiments on thermal diffusion at the Philadelphia Navy Yard deserved a closer look. Abelson was building a plant to produce enriched uranium to be completed by early July 1944. It might be possible, Oppenheimer thought, to help Abelson complete and expand his plant and use its slightly enriched product as feed material for Y-12 until the problems plaguing K-25 could be resolved.
The liquid thermal diffusion process had been evaluated as early as 1940 by the Uranium Committee, when Abelson was still with the National Bureau of Standards. In 1941 he moved his research to the Naval Research Laboratory, where there was more support for his work. During the summer of 1942 Bush and Conant received reports about Abelson’s research but concluded that it would take too long for the thermal diffusion process to make a major contribution to the bomb effort, especially since the electromagnetic and pile projects were making satisfactory progress.
Supporting Thermal Diffusion
After a visit with Abelson in January 1943, Bush encouraged the Navy to increase its support of thermal diffusion. A thorough review of Abelson’s project early in 1943, however, concluded that thermal diffusion work should be expanded but should not be considered as a replacement for gaseous diffusion, which was better understood theoretically. Abelson continued his work independently of the Manhattan Project. He obtained authorization to build a new plant at the Philadelphia Navy Yard, where construction began in January 1944.
(Note: The Navy, and specifically the Philadelphia Navy Yard, was chosen by Abelson because of their experience dealing with huge ship boilers which produced steam. Steam was the essential source of heat required for the liquid thermal diffusion process.)
Groves immediately saw the value of Oppenheimer’s suggestion and sent a group to Philadelphia to visit Abelson’s facility. A quick analysis demonstrated that a thermal diffusion plant could indeed be built at Oak Ridge and placed in operation by early 1945. The steam required in the convection columns was already at hand in the form of the almost completed K-25 power plant (the largest in the world). It would be relatively simple to provide steam to the thermal diffusion plant and produce enriched uranium, while providing electricity for the K-25 plant when it was finished. Groves gave the contractor, the H. K. Ferguson Company of Cleveland, just ninety days from September 27 to bring a 2,142 column plant on line (In comparison, Abelson’s plant in Philadelphia contained 100 columns). There was no time to waste as Happy Valley in Oak Ridge braced itself for a new influx of 10,000 workers.
Building the Plant
Closely patterned on the Navy pilot plant in Philadelphia, the S-50 plant consisted of 2,142 uniform columns, each 48 feet high. Manufacturing this plant to exacting specifications within 90-days would be no small feat. Indeed, 21 firms turned down the assignment before the H. K. Ferguson Company, an engineering firm in Cleveland, accepted the challenge.
The construction of the plant demanded a high level of precision. It required nearly perfectly round columns with a uranium hexafluoride layer spacing of only 0.010 inches (3 sheets of paper) thick! In order to meet the nearly impossible deadline, operators, electricians and welders scrambled to complete the project and even used passenger trains to transport construction materials. In the end, the contractors beat the deadline and completed the S-50 plant in just 69 days.
The S-50 production plant required an enormous amount of energy and was shut down in 1946. The K-25 plant was most effective.
Further Reading
For more information on the Manhattan Project’s sites in Tennessee and the scientists who worked there, please consider purchasing our Guide to the Manhattan Project in Tennessee, which can be found on Amazon. Additionally, WorldCat checks local libraries for copies in your area.
The text for this page was taken and adapted from the U.S. Department of Energy’s official Manhattan Project history: F. G. Gosling, The Manhattan Project: Making the Atomic Bomb (DOE/MA-0001; Washington: History Division, Department of Energy, January 1999), 19-26, 31-32.